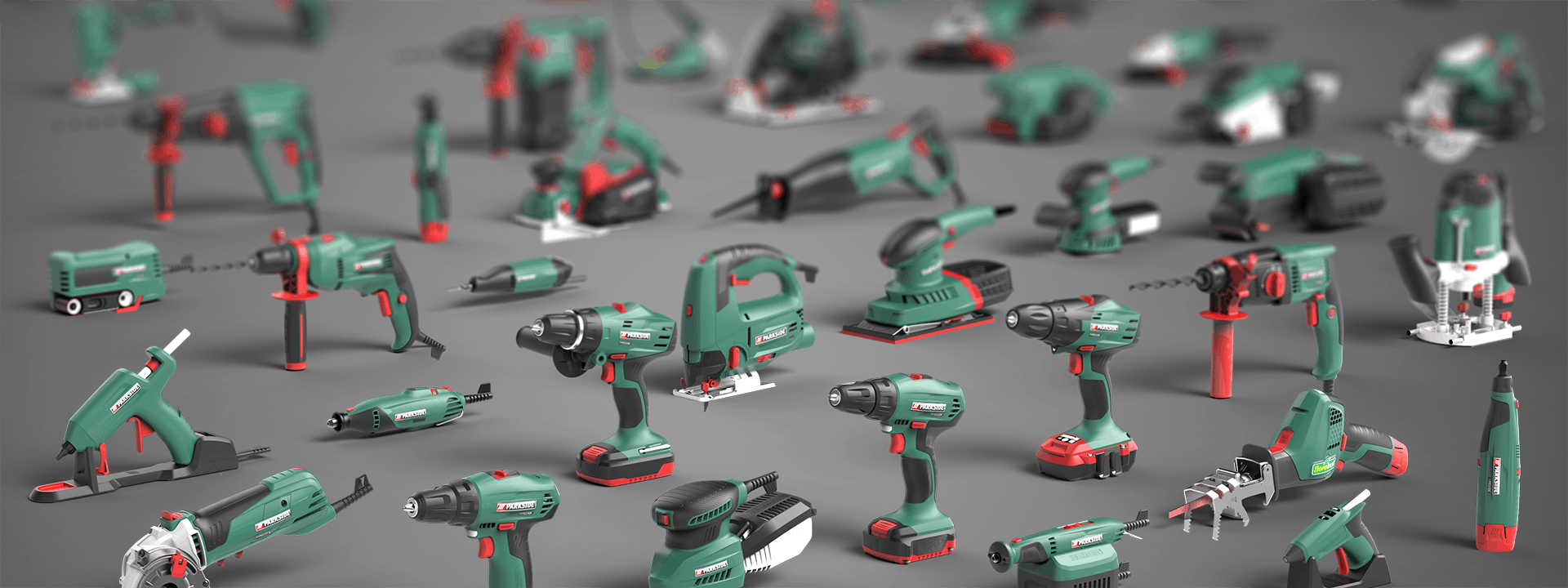
tool design
What we learned from designing over 500 power tools.
- How can we improve the handling of our power tools?
- How do we bring the performance "on the street" or in the workpiece?
- Which design best appeals to our target group?
Over the past 15 years we have dealt with countless such questions. During this period we have developed, improved and launched more than 500 power tools with our customers. Many are currently in development.
What have we learned from our work?
Which stumbling blocks need to be overcome?
Find out here.
Gut gemachtes Werkzeug erfüllt seinen Zweck
The central question we ask ourselves when developing any tool is: What makes it a good product?
The fulfillment of the task is of course the top priority here. A cheap device from the discount has just as much justification as a high-end professional tool.
The occasional do-it-yourselfer who only wants to attach a shelf or hang up a few pictures usually does not push a simple, inexpensive drill to its performance limit. The vast majority of these devices eke out a little-used existence in the closet or basement. The decisive purchase criterion here is the price-performance ratio.
In professional use, on the other hand, effectiveness and speed are important. A failure means an immediate loss of productivity that must be prevented. In this case, performance and robustness are paramount.
Die 5 wichtigsten Anforderungen im Werkzeugdesign
In the development of our power tools, the same evaluation criteria appear again and again: Of course, they are weighted differently according to the respective target group.
The requirements can be divided into the following areas:
1. Reliable function creates occupational safety
Customers often confront us with product weaknesses that need to be analyzed: damaged switches, gear blocks that have broken out of the housing, overheated devices.
It is often not just the engineers who ensure stronger materials or better construction. In many cases we can protect them from damage by cleverly placing controls or sensitive components.
For example, the use of shock-absorbing TPE (thermoplastic elastomer) in sensitive areas can prevent the housing of a cordless screwdriver falling from a ladder from breaking, for example.
On the other hand, a good cooling concept is extremely important, especially when grinding machines are used for longer periods of time.
Intelligent design ensures durability and a high level of safety.
How can excess heat be dissipated efficiently?
With well thought-out ventilation openings planned in the tool design right from the start, as well as, if necessary, with highly heat-conducting metal parts, we can avoid overheating without impairing the user during operation.
This brings us to the second aspect of safe functioning: occupational safety. For each device, we analyze the respective danger areas for the user.
These can be minimized with a wide variety of protective hoods or safety devices, such as multi-way switches that cannot be triggered unintentionally.
We can also often increase the distance between the danger area and the user interface and thus safety by arranging the technical functional and operating elements in an alternative way.
Many such requirements for occupational safety are specified in standards and are taken into account accordingly.
2. Efficient work through intuitive ergonomics
Safety is also achieved through good ergonomics.
I can only work safely if a tool lies securely in my hand.
Only when I can reach the controls where I intuitively expect them can I work in a controlled and efficient manner.
Only when I know what activation state my tool is in can I handle it safely.
To optimize handling, we produce ergonomic models either by hand, using a 3D printer or CNC milling machine.
Of course we have gained a lot of experience, but nothing beats trying it out.
Every new tool design has to be tested; and preferably from as many different people as possible. We always check the ergonomic requirements that the target group or the intended use specify.
- Who operates the machine?
- In what posture does the activity take place?
- Do you work with gloves?
- What burdens arise for the user at work?
Taking into account scientifically and statistically determined body measurements, we determine handle lengths and thicknesses as well as the positions of operating elements in order to ensure that work is as stress-free as possible.
Ergonomics also includes the entire area of operator feedback. The device must give me as much information as possible about operating options and its current status.
At best, this is done using product graphics that are language-neutral, clearly recognizable switch positions, tactile pressure points and clearly visible scales, pointers, LED indicators or displays.
3. Economical production
Economical production is particularly important for products from the do-it-yourself (DIY) sector. Power tools in hardware stores or discounters are sold in the hundreds of thousands.
A material quantity-optimized design plays an important role here. In some cases, a single gram of material savings can decide whether a product is marketable in a competitive environment.
But we also plan the cycle times in injection molding and the simplest possible assembly from the start of the development. The time window for production is often very limited due to the planned market launch date.
The technical production possibilities of the respective manufacturer or supplier must be determined precisely from the start and taken into account in the design. Especially when it comes to production in Asia, you cannot always assume that the technology is state-of-the-art.
From the very first sketches of ideas, we take into account, for example, the demoulding directions of the later production tools. In this way we avoid unnecessary correction loops and changes in development and minimize the time to market (time to market).
4. Sustainable development
Ecological aspects also speak in favor of making the use of materials as economical as possible.
Especially with large quantities, every gram of material saved or the avoidance of potentially harmful substances is an important goal in the interest of the environment and health and is now being pursued very consistently by all our customers.
However, sustainability in development also means bringing the respective product onto the market only when it is mature. Quality management plays a special role here.
During development, we repeatedly check whether planned measures and design details also fulfill their respective purpose and lead to an improvement in the product. Prototypes and pre-production samples are used for control.
This is the only way for the finished product to exist in the market for as long as possible and not have to be replaced prematurely by an improved successor.
Understand product families as a series right from the start
Power tools are usually part of an entire product family or series. When developing a new design, we therefore recommend building the tool design directly as a series with several representative family members.
This is the only way to develop design elements that can be applied to a wide variety of device topologies.
There are static as well as dynamic machines, hand-held or stationary, large or small, elongated or compact constructions. The design should be applicable and, above all, recognizable for all cases with their different peculiarities.
For each individual product, family affiliation should be clearly visible to increase brand identity. Starting the design development with just a single product and continuing it in the same way requires a great deal of adjustment work afterwards in order to achieve a uniform appearance for a product family.
We therefore recommend:
Do the right thing from the beginning!
5. Target group-oriented design
We industrial designers do not design for ourselves or our portfolio. Nor do we design for our customers and their preferences. If we really want to develop a successful product, we have to serve the target group you – our client – have in mind with our design decisions.
In most cases, these are the later end users or experienced buyers. This target group's expectations of the device should ideally be visibly met by its external appearance. Professional functions, durability, robustness, lightness, easy cleaning, intuitive operation, but possibly also certain fashion trends are properties that can be visualized through targeted product design so that everyone understands them intuitively. Craftsmen, high-tech companies, occasional do-it-yourselfers, ambitious DIYers, women (smaller handles, lighter devices...) or children (optical references to topics from the playful environment) all have their own requirements for a tool.
For example, the purchaser of a high-tech bone saw in a hospital will generally prefer a clean tool design with extremely intuitive user guidance. This gives the physician the impression of good cleaning and disinfection suitability and security against incorrect operation.
A craftsman might want to be able to quickly find his cordless screwdriver on a confusing construction site or prevent it from slipping off a sloping roof. He'll prefer a brightly colored device with shock-absorbing rubber bumpers.
CONCLUSION
We have gained a lot of experience in designing around 500 power tools. Only the critical review of the technology package and the development of intuitive ergonomics later enable safe and efficient work and a successful product.
You, as the client, must also make the right strategic decisions in order to derive the greatest possible benefit from the design development for your company.
Machines will become increasingly intelligent in the future. The entry of IT into the power tools area has long since begun. Combinations with measuring technology, smartphones with app control and radio technology already enable fine tuning, statistical evaluations, increased security and protection against theft on the construction site. This development will continue.